A Cleaner Environment - Clean Air
The Australian Government will reach its emissions reduction target through its Direct Action Plan to efficiently and effectively source low cost emissions reductions and improve Australia’s environment. This will be done primarily through our Emissions Reduction Fund.
MORE INFO :
Monday, December 21, 2015
Wednesday, December 16, 2015
hydrocarbon odour
Ideal for Hydrocarbon odours Anotec 0307 is the standard odour control, formulation. Efficacies of the formulation are determined via qualitative and quantitative techniques for odour measurement. Anotec 0307 formulations can be fogged, hand sprayed, misted or drip-fed depending on the application required. Anotec 0307 is fully miscible in water with scientifically chosen and blended surfactants. This blend, when applied via either a misting, fogging device or trigger sprayer bottle, alters the surface tension of the liquid/vapor compound. A key property of the Anotec 0307 formulation is that it modifies the surface properties of chemical odour components. The primary action takes place at the chemical odour and Anotec 0307 interface.
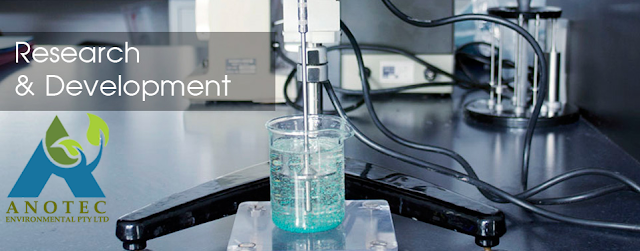
Saturday, November 28, 2015
Friday, November 27, 2015
Brooklyn 'rotting carcass' odour unlawful
by Ben Cameron
A Brooklyn meat rendering company that caused a ‘rotting carcass’ smell so bad it stopped nearby residents from inviting visitors to their homes was found guilty in court on Tuesday.
Australian Tallow Producers was found guilty of three counts of air pollution offences in the Melbourne Magistrates’ Court following an Environment Protection Authority Victoria investigation.
The company was found to have breached the Environment Protection Act 1970 after it polluted the atmosphere with odours offensive to humans on three separate occasions in June 2011 and September 2011.
ATP operates a rendering facility and manufactures tallow from mixed abattoir material on Geelong Road, Brooklyn.
On 22 June 2011, EPA received 13 complaints from nearby residents complaining about offensive odours coming from the site.
Complainants described the odour as a “smell like sewerage, like rotting carcass…”, a “very, very strong putrid dead animal smell…’’ which made one complainant say they felt like throwing up.
Another resident said they “had to lock all the doors and windows and could not have any fresh air in the house”.
The EPA received similar complaints the following day, and on September 21.
An EPA officer, who visited the area on 22 June 2011, reported a strong offensive odour comprising of a mixture of ‘manure, blood, bone and tallow’ coming from ATP’s premises.
Further visits by EPA officers on June 23, 2011 and September 21, 2011 confirmed the stench, with one officer reporting they “felt close to vomiting”.
The company will be sentenced on December 21, 2015.
EPA Chief Executive Officer, Nial Finegan said the EPA called on 11 witnesses, two expert witnesses and nine environment protection officers to give sworn evidence.
“The outcome is a win for the Brooklyn community who have had to put up with localised pollution issues for too long,” he said.
“No community should have to live with an odour so horrid that they can’t even have guests over, constantly feel nauseous and are forced to close their windows.”
The EPA had also issued ATP four pollution abatement notices since 2011 and were fined more than $7000 over an odour incident in 2013.
A Brooklyn meat rendering company that caused a ‘rotting carcass’ smell so bad it stopped nearby residents from inviting visitors to their homes was found guilty in court on Tuesday.
Australian Tallow Producers was found guilty of three counts of air pollution offences in the Melbourne Magistrates’ Court following an Environment Protection Authority Victoria investigation.
The company was found to have breached the Environment Protection Act 1970 after it polluted the atmosphere with odours offensive to humans on three separate occasions in June 2011 and September 2011.
ATP operates a rendering facility and manufactures tallow from mixed abattoir material on Geelong Road, Brooklyn.
On 22 June 2011, EPA received 13 complaints from nearby residents complaining about offensive odours coming from the site.
Complainants described the odour as a “smell like sewerage, like rotting carcass…”, a “very, very strong putrid dead animal smell…’’ which made one complainant say they felt like throwing up.
Another resident said they “had to lock all the doors and windows and could not have any fresh air in the house”.
The EPA received similar complaints the following day, and on September 21.
An EPA officer, who visited the area on 22 June 2011, reported a strong offensive odour comprising of a mixture of ‘manure, blood, bone and tallow’ coming from ATP’s premises.
Further visits by EPA officers on June 23, 2011 and September 21, 2011 confirmed the stench, with one officer reporting they “felt close to vomiting”.
The company will be sentenced on December 21, 2015.
EPA Chief Executive Officer, Nial Finegan said the EPA called on 11 witnesses, two expert witnesses and nine environment protection officers to give sworn evidence.
“The outcome is a win for the Brooklyn community who have had to put up with localised pollution issues for too long,” he said.
“No community should have to live with an odour so horrid that they can’t even have guests over, constantly feel nauseous and are forced to close their windows.”
The EPA had also issued ATP four pollution abatement notices since 2011 and were fined more than $7000 over an odour incident in 2013.
Thursday, November 26, 2015
Shell Canada fined C$825,000 for 2013 refinery odour leak
Shell's company logo is pictured at a gas station in Zurich April 8, 2015. REUTERS/Arnd Wiegmann
CALGARY, Alberta (Reuters) -
The Ontario government on Tuesday ordered Shell Canada, a wholly owned subsidiary of Royal Dutch Shell , to pay C$825,000 (£546,727) in fines for discharging a contaminating odour from its Sarnia refinery in 2013.
In a statement, the Ontario Ministry for Environment and Climate Change said Shell had pleaded guilty to one offence of permitting a discharge of an odour containing mercaptan, a foul-smelling gas.
The Shell Sarnia Manufacturing Centre is located in Corunna, Ontario, and on Jan. 11, 2013, employees discovered a leak from a line containing mercaptan, which flowed into an on-site ditch that empties into the refinery's storm sewer system.
The odour affected a number of people in the nearby Aamjiwnaang First Nation, with several complaining of sore eyes and throats, headaches, nausea and vomiting.
Shell was fined C$500,000 for the offence, plus a victim surcharge of C$125,000 and ordered to donate C$200,000 to the Aamjiwnaang First Nation.
(Reporting by Nia Williams; Editing by Cynthia Osterman)
Wednesday, November 25, 2015
In this ever-changing society, the most powerful and enduring brands are built from the heart. They are real and sustainable. Their foundations are stronger because they are built with the strength of the human spirit, not an ad campaign. The companies that are lasting are those that are authentic
In this ever-changing society, the most powerful and enduring brands are built from the heart. They are real and sustainable. Their foundations are stronger because they are built with the strength of the human spirit, not an ad campaign. The companies that are lasting are those that are authentic
Tuesday, November 24, 2015
GREENWICH-MOHAWK REMEDIATION: Odour woes halt excavation work
Excavation work has been halted in a concentrated area of the Greenwich-Mohawk brownfield remediation site after intense odours were generated over the past two days.
The city announced Wednesday that cleanup work at the north end of the site at 347 Greenwich St. was stopped due to smells emanating from a heavy concentration of petroleum hydrocarbons. The odour had been magnified due to unseasonably mild temperatures combined with humidity and dense fog overnight Tuesday, according to a media release from the city.
On Wednesday morning, two large hand-painted signs on plywood were spotted propped up near the brownfield site, bemoaning the ongoing odour resulting from remediation work.
Red painted letters on one read: "How sick R we of the smell," while a second read: "Please stop. Fumes R making us sick."
The bad smells, which vary in description from heavy oil or asphalt to electrical or burning smells to a chemical stink, first became an issue in July. The stench results from excavation work in an area heavily contaminated by oil or petroleum hydrocarbons over many decades by industries long gone.
Residents in the Eagle Place and Echo Place neighbourhoods have complained about smells permeating their homes and of being unable to enjoy their properties as well as suffering from headaches and sore throats.
One Mohawk Street resident, who preferred her name not be used, said the recent worsening of the odour became "super strong" on Tuesday night.
"I got up this morning and I could still smell it in my garage," she said Wednesday morning.
"People are really tired of it," she said.
The resident said the city has done a good job of keeping neighbours informed and she understands that "before things get better they'll have to get worse."
On Wednesday, the city announced it was taking action to decrease the impact on area residents.
Excavation activities on the concentrated area were halted until further notice. And as of late Tuesday efforts have been focused on odour management and excavation on other areas of the site, further from neighbourhood properties.
The city said that an additional vacuum truck will remain on site and be dedicated to oil skimming operations.
As well, additional daily applications of odour suppressing foam will be used on problem surfaces, including stockpiles and excavation slopes.
The city also announced that it will reassess the work program to ensure that heavily concentrated areas are excavated at a future date when warm temperatures do not worsen odours.
Ministry of Environment representatives visited the site on Oct. 29 in response to odour complaints caused by high winds and a large volume of rain that fell on Oct. 28, said city spokesperson Maria Visocchi.
Officials confirmed that air quality levels remain consistent with ministry standards and all volatile organic compounds data collected to date is within ministry guidelines, she said.
Daily air monitoring is scheduled to continue through November.
As of Nov. 1, 83,000 cubic metres of soil had been treated either through bioremediation or a coarse material wash treatment, according to the city. In addition more than 100,000 litres of oil has been skimmed from the excavation water and recycled.
Last week, area residents also were notified via a letter in their mailboxes of work being done in the northeastern portion of 22 Mohawk St. involving the removal of a small area of xylene-impacted material. Xylene is a solvent found in petroleum, gasoline, coal and wood tar.
The material was taken to 66 Mohawk St. to be treated. That work was estimated to last two to three days and may have resulted in a "magic marker" smell to the air, according to the city.
Additional monitoring of air quality levels was conducted during that work and it was possible that workers in the immediate excavation area would be required to wear respirators, stated the letter to residents. Air monitoring indicated that no applicable ministry standards were exceeded, the city said.
Odour issues have been a concern since July, but smells became overpowering in September when workers hit a heavily contaminated oil pocket at 347 Greenwich St. The oil was nearly a quarter-inch thick. Excavation work was then temporarily stopped and workers concentrated on cleaning efforts and odour control.
The Greenwich-Mohawk site was once home to come of the city's biggest and best-known factories, including Massey, Cockshutt and Sternson. The site was heavily contaminated and the city is conducting a massive cleanup operation.
Remediation is expected to continue to the end of March but if more work is needed, it may continue to the end of December 2016.
The city announced Wednesday that cleanup work at the north end of the site at 347 Greenwich St. was stopped due to smells emanating from a heavy concentration of petroleum hydrocarbons. The odour had been magnified due to unseasonably mild temperatures combined with humidity and dense fog overnight Tuesday, according to a media release from the city.
On Wednesday morning, two large hand-painted signs on plywood were spotted propped up near the brownfield site, bemoaning the ongoing odour resulting from remediation work.
Red painted letters on one read: "How sick R we of the smell," while a second read: "Please stop. Fumes R making us sick."
The bad smells, which vary in description from heavy oil or asphalt to electrical or burning smells to a chemical stink, first became an issue in July. The stench results from excavation work in an area heavily contaminated by oil or petroleum hydrocarbons over many decades by industries long gone.
Residents in the Eagle Place and Echo Place neighbourhoods have complained about smells permeating their homes and of being unable to enjoy their properties as well as suffering from headaches and sore throats.
One Mohawk Street resident, who preferred her name not be used, said the recent worsening of the odour became "super strong" on Tuesday night.
"I got up this morning and I could still smell it in my garage," she said Wednesday morning.
"People are really tired of it," she said.
The resident said the city has done a good job of keeping neighbours informed and she understands that "before things get better they'll have to get worse."
On Wednesday, the city announced it was taking action to decrease the impact on area residents.
Excavation activities on the concentrated area were halted until further notice. And as of late Tuesday efforts have been focused on odour management and excavation on other areas of the site, further from neighbourhood properties.
The city said that an additional vacuum truck will remain on site and be dedicated to oil skimming operations.
As well, additional daily applications of odour suppressing foam will be used on problem surfaces, including stockpiles and excavation slopes.
The city also announced that it will reassess the work program to ensure that heavily concentrated areas are excavated at a future date when warm temperatures do not worsen odours.
Ministry of Environment representatives visited the site on Oct. 29 in response to odour complaints caused by high winds and a large volume of rain that fell on Oct. 28, said city spokesperson Maria Visocchi.
Officials confirmed that air quality levels remain consistent with ministry standards and all volatile organic compounds data collected to date is within ministry guidelines, she said.
Daily air monitoring is scheduled to continue through November.
As of Nov. 1, 83,000 cubic metres of soil had been treated either through bioremediation or a coarse material wash treatment, according to the city. In addition more than 100,000 litres of oil has been skimmed from the excavation water and recycled.
Last week, area residents also were notified via a letter in their mailboxes of work being done in the northeastern portion of 22 Mohawk St. involving the removal of a small area of xylene-impacted material. Xylene is a solvent found in petroleum, gasoline, coal and wood tar.
The material was taken to 66 Mohawk St. to be treated. That work was estimated to last two to three days and may have resulted in a "magic marker" smell to the air, according to the city.
Additional monitoring of air quality levels was conducted during that work and it was possible that workers in the immediate excavation area would be required to wear respirators, stated the letter to residents. Air monitoring indicated that no applicable ministry standards were exceeded, the city said.
Odour issues have been a concern since July, but smells became overpowering in September when workers hit a heavily contaminated oil pocket at 347 Greenwich St. The oil was nearly a quarter-inch thick. Excavation work was then temporarily stopped and workers concentrated on cleaning efforts and odour control.
The Greenwich-Mohawk site was once home to come of the city's biggest and best-known factories, including Massey, Cockshutt and Sternson. The site was heavily contaminated and the city is conducting a massive cleanup operation.
Remediation is expected to continue to the end of March but if more work is needed, it may continue to the end of December 2016.
Charlton residents rally over abattoir odour, disease fears
Andrew Backhouse | 30th Oct 2015 5:00 AM
A GROUP of residents with concerns about a proposed meat processing facility on the outskirts of Toowoomba is holding a community meeting tonight. FKG Group is planning to build an $80 million abattoir in the Witmack Industrial Park about 10km west of Toowoomba. A development application is before Toowoomba Regional Council. The public notification stage ended on September 22. Speaking on behalf of residents, Chrissie Bach said in their view the development did not belong in its proposed location, which is zoned for medium impact. She said neighbours of the proposed facility were worried about offensive odours and the impact they would have on future development in the Charlton precinct. Ms Bach also raised concerns about alleged health risks. Toowoomba union delegate Chris McGaw and Oakey veterinarian David Pascoe have publicly raised noise, odour and planning concerns about the project. FKG Group manager of property development Dallas Hunter has defended the project saying the state-of-the-art design would ensure that the facility would have little to no impact on nearby residents. "It's just as important for us and our neighbours that we have a low-impact or nil-impact plant and that's what we're designing," he said.
More info Here
A GROUP of residents with concerns about a proposed meat processing facility on the outskirts of Toowoomba is holding a community meeting tonight. FKG Group is planning to build an $80 million abattoir in the Witmack Industrial Park about 10km west of Toowoomba. A development application is before Toowoomba Regional Council. The public notification stage ended on September 22. Speaking on behalf of residents, Chrissie Bach said in their view the development did not belong in its proposed location, which is zoned for medium impact. She said neighbours of the proposed facility were worried about offensive odours and the impact they would have on future development in the Charlton precinct. Ms Bach also raised concerns about alleged health risks. Toowoomba union delegate Chris McGaw and Oakey veterinarian David Pascoe have publicly raised noise, odour and planning concerns about the project. FKG Group manager of property development Dallas Hunter has defended the project saying the state-of-the-art design would ensure that the facility would have little to no impact on nearby residents. "It's just as important for us and our neighbours that we have a low-impact or nil-impact plant and that's what we're designing," he said.
More info Here
Egg farm odour will hit residents of West Belconnen, says Parkwood owner
Parkwood Eggs in Belconnen is worried the smell from its laying sheds will affect residents of a planned new suburb.
Parkwood Eggs in Belconnen is worried the smell from its laying sheds will affect residents of a planned new suburb. Photo: Jeffrey Chan
The owner of Parkwood Eggs has slammed the West Belconnen housing development as way too close for comfort, indicating that much of the proposed new housing will be affected by smell from the barn egg farm.
Pace Farm chief executive Paul Pace says the business will probably be forced out of Canberra when its lease expires if the new suburb goes ahead, with the loss of 65 primary production jobs.
He described the proposed clear zone of 750 metres around the Parkwood Egg farm as completely inadequate.
But the company's claims were rejected on Friday by the Land Development Agency, whose deputy chief executive, Ben Ponton, said there would be no smell for residents outside the 750-metre buffer and when development began inside the buffer the egg farm lease would be cancelled.
Planning Minister Mick Gentleman has approved a territory plan change to pave the way for the housing development, which will have 11,500 homes, spilling over the border into NSW. The development has sparked concerns about the impact on the adjacent Ginninderra Falls area.
Mr Gentleman approved the Territory Plan variation without referring it to the ACT Parliament's planning committee, a decision described as disappointing by Liberal planning spokesman Alistair Coe.
The West Belconnen development area, earmarked for 6500 homes. Parkwood is in the top right of the development area, near the border with NSW and in part of the zone coloured pink.
The West Belconnen development area, earmarked for 6500 homes. Parkwood is in the top right of the development area, near the border with NSW and in part of the zone coloured pink. Photo: Supplied
"What is the purpose of having a planning committee if it is not to consider massive housing estates?" Mr Coe said.
Pace Farm commissioned a report from Katestone Environmental, which concluded the government's report had significantly underestimated the odour emissions from the egg farm – and could be out by a factor of more than seven.
A clearance zone of between three and four kilometres was necessary to meet NSW odour guidelines and reduce the impact on residents to an acceptable level, Pace Farm said.
In NSW, a developer would be required to carry out high-level modelling, especially when the plan was to rezone land "to permit some 30,000 people to reside in the vicinity of the largest poultry farm in the region", it said.
Pace has seven sheds with 189,000 chickens, but permission for as many as 10 sheds, housing 270,000 chickens.
The Katestone report said the government-commissioned odour report had assumed an odour emission rate of 4 OU ("odour units") per minute per bird, but that significantly underestimated the emissions from layer chicken farms, which could be up to 7.6 times higher.
And while the government report had used a Victorian guideline of 7 OU in the absence of a Canberra limit, it would have been more logical to use the NSW limit of 2 OU.
Whichever limit was used, both were exceeded at distances greater than 750 metres from the Parkwood farm in all directions except the north to north-east, Katestone said. To meet the NSW odour figure, the buffer should be three to four kilometres from the farm. To meet the Victorian figure, the buffer should be 2.5 to three kilometres.
Mr Pace said Pace had recently switched from cage to barn eggs at the ACT farm, which also housed one of the company's three grading and packing centres nationwide. The Parkwood lease runs for another 18 years and Mr Pace said he had expected the business to remain on site for as many as 50 years, but his discussions with the government suggested the lease was highly unlikely to be renewed because the farm was incompatible with residential development.
Mr Ponton confirmed that Parkwood's lease would not be renewed at the end of 18 years, and might be resumed earlier if the housing development went more quickly than anticipated. Parkwood was "absolutely" aware of that.
"Parkwood Eggs know and has done for some time that the land is required for development in the next 20 years," Mr Ponton said. "They know what the rules of engagement are."
The government rejected Parkwood's analysis, he said. The current Crown lease specified an exclusion zone of just 500 metres. The government-commissioned report had recommended 600 metres. And the decision to impose a 750-metre zone had been based on best-practice South Australian guidelines.
Pace's concerns were set out in a submission to the Territory Plan change, but the government said an independent site auditor had endorsed the approach, it said.
Riverview plans to sell the first property off the plan in June 2016, with residents living in the new suburb in the third quarter of 2017.
Monday, August 10, 2015
The Benefits of Clean Water
The benefits of clean water and having plenty of safe water to drink are well known. Most of us have experienced the feeling of not getting enough water; when we feel sluggish and light-headed from being dehydrated.
Many common health problems can be avoided by all of us if we simply drink more water.
Staying hydrated and drinking plenty of water helps to flush out wastes from our bodies.
Water is a transport medium for the nutrients our bodies need.
Body temperature (perspiration) is regulated by the amount of available water in our bodies.
Water also regulates the pH balance and supports a multitude of physiological processes.
Being well hydrated elevates our energy levels and can help alleviate headaches.
Severe dehydration causes a multitude of health problems, not the least of which are fatigue, depression, diabetes, high blood pressure, weakness, and loss of energy.
But some people have plenty of water to drink. Take the rain forest, for instance. Water is everywhere, but people still suffer from a lack of safe, clean water. The water they find to drink is often unsafe for them to consume. See "Water-borne Diseases"
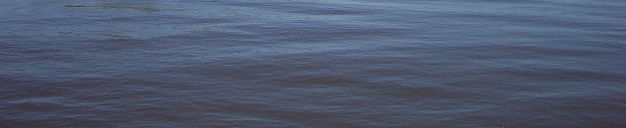
So what they need is not just any water, but they need to experience the benefits of clean water! Clean, clear and safe water.
So, what do we mean when we use the term "clean water"? In the context of this website, we are referring to water that is safe for human consumption. “Safe” water is also a good definition. Safe water must be free from disease-causing pathogens. But water that is free of pathogens may still be clouded by sediment.
Water that is fit for human consumption must be clean and clear. It must be water that does not have offensive odor or color, making it undesirable and unpalatable, and deterring people from drinking it. It must be desirable to drink it and people must have confidence that they can give it to their family with certainty that they are giving them water that is fresh, clean, clear, healthy and safe.
Access to safe, clean water opens up a world of possibilities for community development. Without water, the most basic element of life, all other development efforts will hit a brick wall.
Sanitation and hygiene, working together with a source of clean water create lasting community health and sustained human growth and development.
Just the simple act of washing hands with soap can reduce the incidence of diarrheal disease. When coupled with the use of adequate sanitation facilities and a dependable source of clean water, the multiplied effects are even greater.
As a child, disease from lack of water, sanitation and hygiene carries over into the schoolhouse. A child’s education is affected by an increase in absenteeism, decrease in cognitive potential, and increased attention deficits. Young girls often stop going to school if the school lacks adequate sanitation facilities.
With the benefits of clean water, adequate sanitation, and good hygiene in place, educated individuals grow up to be enterprising adults, who become the owners of businesses, as well as corporate, community and national leaders.
From the early years of life, throughout childhood and into adulthood, water is the common beneficial factor determining the quality of life and the possibilities of the future.
Friday, July 03, 2015
EKOSyme for use in ponds
Organic based technology providing a non toxic alternative to treating ponds polluted with waste.
This formulation is a proprietary Nano array of nutrients, enzymes, bacteria, biosurfactants and bio oxygen catalysts.
By treating the area with the EKOsyme , BOD will be reduced by increased oxidation. Allowing for odours to be reduced and the water used in agriculture.
Usage through various application methods including our proprietary mechanisms, rule of thumb 10 litres of our EKOSyme solution to 60,000 L of pond volume.
For best and immediate results it is best to use our proprietary application system and applied according to our recommendation this will result in immediate (over a 24 hr. period) BOD reduction result.
For continual treatment is suggested
Monday, June 01, 2015
Can Exercise Really Make You A Better Leader?
What does building your body have to do with building organizations and people?
After cultivating a life-long passion and habit for a fitness regimen as well as an always on, “watch-what-you-eat” discipline, let me give you my personal opinion in one word:
Everything.
Here’s the deal. You can get the science-backed detail and the case for exercise anywhere on the internet. Launch into a Google search for “why should I exercise” and see all of this.
Instead, let me outline some of the reasons why being fit will make you a better leader.
As an advisor helping top executives solve strategic growth challenges in their businesses and teams, I often find myself reminding leadership of the importance of personal and professional growth as a significant precursor to organization growth. In other words, people growth drives business growth – not the reverse.
There is a ripple effect that personal growth has on the engagement, confidence and ambition that employees bring to their work. Leadership is the spark to ALL of it. If it’s not happening, recognized or talked about in your workplace, it’s on you.
A big piece of the puzzle in driving folks to own their personal development is encouraging an exchange of bad habits for good. Exercise is an easy win.
If you’re driven to make a mark in leadership, here’s my case for why being fit will not only elevate your impact but fundamentally change the trajectory of growth for the people whom you lead:
It Creates Energy and Stamina. Counterintuitively, you need to use energy to get more of it. This is why a person who sleeps a lot can still complain of being tired. After years of developing an afternoon exercise habit, I still find myself exercising at the end of the day. I can feel tired enough at the end of the day to go right to sleep; however, after exercising, find it hard to get to sleep. Exercise creates energy. It makes a huge difference when you’re leading people and families, doesn’t it?
It Fuels Focus. In a world brimming with distraction and demands at every turn, there are very few activities left that allow a complete disconnect. Exercise removes your mind from the screens, calls, and multi-tasking. Quite amazingly, you’ll find your thoughts and focus during exercise settling on the most important priorities in your life. This has happened to me countless times – when I start an exercise session, it’s not uncommon to have a mind racing with lots of to-do’s, tasks, worries, etc, only to see all of that whittled down to virtually nothing 30-45 minutes later. Following exercise, I have a mind clear and focused, ready for action.
It Drives Confidence. most effective and influential leaders exude confidence. If we’re not confident in ourselves, it’s impossible to express or have confidence in others. Being fit builds self-confidence and self-esteem. Leaders with low self-esteem can bring a defensive posture, a failure to recognize others or encourage mistakes, as well as a curt tone that discourages idea sharing into the workplace, unknowingly stifling the growth of others. As exercise begins to have positive change on our bodies, it shows up in the mirror and through compliments from those around you. As you start to feel better about yourself, confidence shows up at home and in the office. And so does a different attitude. This changes everything.
It Unlocks Influence. Exercise releases key hormones in your brain that reduce stress and anxiety. We all have become accustomed to heavy bouts of daily stress which impact us personally, but more critically, the people around us. As leaders, unmanaged stress can have adverse affect on our relational skills with people, detracting from our influence. An exercise session can quickly deflate heavy stress, leaving you calm, cool and collected to be at your influential-best with people who matter.
It’s Contagious. People who have successfully transformed their physical and emotional shape are admired, as it requires fortitude, discipline and perseverance. The achievement alone can inspire others, but more importantly, it establishes an example for personal growth that others will aspire-to or want to follow. As more people around you begin to latch onto a movement for better health, the accountability to a ‘new normal’ grows larger on the culture as a whole.
It’s a Spark to Creativity. Hands-down, my very best thinking and idea time happens while exercising. As mentioned above, exercise has an incredible releasing effect, helping us to de-stress and prioritize in our lives. This calming and clearing-effect opens our minds and hearts to possibility-thinking which is a spark to creative ideas. Imagine an entire workforce engaged in this mode of thinking!
It Triggers the Right Habits. When hard work pays off, it’s rewarding. Exercise is no different. If you’re looking for a starting point to big change, exercise is it. Building lean muscle mass and cardiovascular health is the sustainable path to long-term health. As you begin to feel physically and emotionally transformed, the positive results hardwire exercise as a habit. Generally speaking, we all want more of a good thing, right? Exercise is a spark to other healthy habits; most commonly, better nutrition and eating habits. Subconsciously, the more we exercise and improve our health, the less we want to do anything to damage the strong body we are building. Very rarely do you see a person leaving a gym lighting a cigarette? Could it be that a good habit can replace a bad habit?
It’s Not About Us. Our bodies were designed for activity. This is why they hurt, get sick, or are rendered immobile if we aren’t active enough. You and I have been given only one body for the life and time we have here on earth. You’ve also been called to be a leader over your organization and your family. There are people everywhere who need you to lead them. And that means you need to be here so you can lead them. So, in the end, fitness is not really about us. And…neither is leadership.
If you’re already into being fit, you’re certainly enjoying the benefits that I mention above. If you’re not, what’s keeping you from getting started?
How valuable would it be to you to start a fitness program tomorrow?
Most importantly, what kind of leader might you become to the people in you’re life who matter most, at the office and at home?
You’ve been called. They need you. To be here.
Now – go be fit!
You’ll be glad you did. And so will they.
Sunday, May 24, 2015
Green chemistry: understanding barriers and opportunities
We have a long way to go to mainstream green chemistry. Now in its 10th year, the Green Chemistry and Commerce Council (GC3), a network of some 70 companies across sectors and supply chains, has undertaken a number of projects, aimed at supporting dialogue and model collaborations that advance research, development and adoption of green chemistry solutions.
These efforts have helped to: establish approaches to enhance chemical information flow, through supply chains, while protecting confidential business information; support informed decision making through supply chains on alternatives to priority chemicals; educate professionals across firms on the fundamentals and value of green chemistry and adoption models; connect firms across sectors to learn from each other’s challenges, and approaches to overcoming them; and support funding for research and development in green chemistry.
Ten years ago, major barriers that we identified were resistance to change, concerns about lower performance of green chemistry solutions, lack of data to make the business case, lack of good information through supply chains, and uncertainty about what we mean by green chemistry. While some of these have been addressed over the past ten years, several still remain. A survey of GC3 members in 2014 identified a number of practical impediments including the high cost of research and scaling of green chemistry solutions and the lack of technically, and economically, viable options.
To better understand the barriers to, and opportunities for, accelerating green chemistry, and to build its “Agenda for Mainstreaming Green Chemistry”, the GC3 commissioned three reports for its 10th annual innovators Roundtable, held in April at Nike, Inc:
Making the business and economic case for green chemistry (Released on 5 May). Co-sponsored with the American Sustainable Business Council and undertaken by the consultancy Trucost, this explores the business and value of green chemistry through document review, interviews with key experts, and data analysis;
Barriers to green chemistry adoption and means to accelerate growth along the supply chain (to be released in June). This report, researched by chemical industry experts T Fennelly & Associates, identifies, through more than 50 interviews and document analysis, nine key deterrents to growth as well as four accelerators to more effectively drive it; and
Measuring progress towards green chemistry (to be released in June). This white paper, drafted by Environmental & Public Health Consulting, examines the landscape of different types of metrics that can and are being used to measure progress and proposes ways they can enhance this.
These three reports, combined with 10 years of cross-sectoral dialogue in the GC3, note that the opportunities for adoption are promising but activity in this space is sporadic and mostly in reaction to some identified problem, rather than part of a comprehensive innovation strategy. A number of key barriers still exist, including:
- the lack of robust analyses and data on economic opportunities and risks, specific to adoption on an industry-wide scale;
- limited, widely used metrics to evaluate progress in research and adoption;
- supply chain complexity, which creates fragmentation of demand for innovations by application, volume, specification, customer expectation and geography. Complex supply chains also create a barrier to change because they have established infrastructures, strong supplier-customer relationships and mature cost positions;
- incumbency, where existing industry infrastructure is so efficient that it is hard for new entrants to compete with the established supply chain;
- price/performance, where existing chemicals have set the standard. In other words they work well and are cost competitive. This becomes a greater barrier when the sustainability heads of brands or retailers ask for new, more sustainable options but the sourcing decision makers in the same organisation want those options at similar or lower cost;
- concerns about switching risk, where changing to green chemistry alternatives could lead to market failures, such as market loss due to a product’s poor performance, brand tarnishing and other hidden costs, such as changes to process or equipment, material incompatibility, workforce training, or customer education;
- lack of demand, where there is not enough, real or perceived, to make increased production worth the investment and where stakeholders are cautious to move forward to commit to demand or supply; and
- market confusion, where conflicting information from studies and research, policy uncertainties and lobbying efforts lead to the value and risks of a green chemistry investment being unclear.
While the challenges are real, these research efforts and dialogue have identified a number of enablers, many of which are related to addressing supply chain misalignment, including:
- increasing consumer awareness, particularly that of large institutional consumers and retailers – has been a significant driver of demand for safer chemistries. In the future, these large consumers need to have a greater understanding of the options available or on the horizon as well as realistic expectations of the process of developing and gaining required approvals and certifications for new chemicals;
- developing smart policies. If these are well-designed, both supportive and restrictive, they can provide important incentives for green chemistry development, adoption and scale. For example, the proposed Sustainable Chemistry Research and Development Act would establish an advisory committee and action agenda for incentives, technical and information support, collaborations, demonstration, and education;
- increasing collaboration and partnership across the value chain, including give and take (compromise). Addressing supply chain misalignment will require improved communication and joint working, at the earliest stages possible. This can help address issues such as cost and risk sharing, performance expectations, and demonstrating demand. Business to business collaboration needs to be supplemented with enhanced academic-business partnerships and mechanisms to link those with green chemistry challenges with those who might provide solutions;
- using market forces effectively to drive innovation. Recent efforts in the health care, building and retail sectors demonstrate the important leverage that large purchasers have. For example, the GC3 has convened a group of seven major retailers (the Retailer Leadership Council) to engage in dialogue with large chemical manufacturers to accelerate development of green chemistry solutions for priority chemical functions. Brands, for example, in the footwear and apparel sector, can also collaborate in a pre-competitive space to drive innovative solutions;
- understanding and informing the marketplace. Research is needed to better understand market forces and where they may be leveraged to the benefit of green chemistry, through knowledge of costs, barriers, policy and trends in demand, and workforce needs. Additionally, getting the right kind of information – on green chemistry solutions, incentives, success stories, etc - to the people who need it, such as supply chain actors and policy makers can help spur informed actions;
- developing better data and narratives and a more consistent metric: there is a clear need for data to make a strong business case. This includes quantifiable economic and health-related data, but also case examples that provide both transferable models and compelling evidence of successes. A more effective set of metrics can help better characterise momentum towards mainstreaming green chemistry; and
- educating the next generation of leaders and champions in green chemistry. Building a cultural and institutional change will require significant changes in education – both within firms (and supply chains) and university training for scientists (as well as other disciplines) so that they can understand and evaluate how chemical design affects health and environment and are able to work in multi-disciplinary teams to solve product and material challenges, applying green chemistry techniques.
Recent research, and ten years of collaborative projects through the Green Chemistry and Commerce Council, have demonstrated that there is increasing energy and commitment toward mainstreaming green chemistry. The challenge is now in channelling that energy towards a strategic and integrated vision.
While green chemistry may not yet be mainstream, the tools and approaches to getting there are evolving: cross-sectoral, value chain collaboration is growing; innovative new chemistries and materials are being developed; and education and awareness are progressing. The challenge for the coming years will be to move from niche to scale.
anotec environmental
anotec environmental
Monday, May 18, 2015
alert
IDENTITY THEFT (1/2): If you’ve ever had your identity stolen, you’ll know the impact can be financially and emotionally...
Posted by NSW Police Force on Sunday, 17 May 2015
Thursday, May 14, 2015
Odour management is key to anaerobic digestion plants
For the anaerobic digestion (AD) sector to flourish, two key principles need to be addressed. First, the Government needs to enforce the diversion of food waste from landfill and incineration. Second, existing AD facilities must be designed with the best available technology and to the best operational standards. Biffa is running Europe’s largest food waste processing AD facility. Its energy deal with Sainsbury’s Cannock store allows the retailer to be powered by its own food waste using an electricity cable direct from the AD plant in Poplars.
This project brought the plant under the national spotlight and cemented its status as one of the UK’s most influential green ventures. When the company took over the facility from its building and commissioning contractors, it was falling well short of its contractual requirements for odour control. The biofilters designed and built to treat odorous air from the plant were not fit for purpose, and created a focal point of dissension from residents and the regional Environment Agency (EA) team. As any operator of a waste facility will know, protecting neighbours from unwanted environmental effects is a crucial part of fostering acceptance and responsible long-term engagement with local residents and businesses. In the Poplars case, residents – some of whom lived just 200m from the plant – were disappointed about the level and frequency of odour escaping from the plant. Biffa was thereby obligated to develop a robust and bespoke solution for long-term community harmony. With board-level commitment from Biffa to invest in an exemplar facility, we had the in-house skills to make it happen.
The EA had no template or predefined standards for an odour management plan for AD, so it took the company’s in-house engineering team to come up with the solution. Poplar AD 1 They researched across other industries to establish best practice in technologies and management procedures, gradually drafting the odour management plan step-by-step. Sampling and testing each possible source of odour, and then benchmarking against best available technologies, the team finally engineered a robust odour management system for the Poplars site. Biffa invested in a novel vortex scrubber system which uses a combination of speed, turbulence and moisture to separate volatile organics (odorous compounds) from the air stream.
The removal rate of the vortex scrubber is far superior to that of a conventional scrubber: its installation made a significant and lasting improvement. Pre-treated air from the vortex scrubber was then passed to the main odour control treatment plant, providing a double barrier to odour escape. While this provides an effective abatement solution, further works were needed to ensure robust 24/7 operations.
Once the new scrubber was installed, addressing any remaining odour followed the law of diminishing returns. The team introduced systems, procedures and equipment to tackle the challenge. There was no single cure, so the final plan included aspects of training, housekeeping, instrumentation, controls, maintenance and system management. Despite the years of challenging problems,
Biffa has addressed the issues head on, investing a further £4m in process improvements at Poplars. This demonstrates the value that the company places on this flagship facility. The conditions and checks set out in the detailed odour management plan ensure that the plant operates to the highest possible standards and achieves mini-mal impact on the local environment. The Poplars team is now proud to have received zero compliance assessment reports from the EA in the past 12 months, as well as a dramatic fall in odour complaints.
Poplar AD 2 Taking three years and 15 drafts, the odour management plan was finally approved by the EA in March 2015. The improvement has elevated Poplars AD to a ‘best in class’ status with the EA. It is a UK first for such a facility and sets an example for others in the industry to follow. Lisa Pinney, EA area manager for West Midlands, said: “Biffa has made significant investment at the Poplars site. Through 2014, the AD plant has operated not only in line with its permit but also best practice for the industry, which shows what can be achieved when we work together well.” The Poplars management plan is now being used as a template for Biffa’s mechanical biological treatment facility in West Sussex, and is publicly available on the EA website for other AD developers and operators to learn from. Following this experience, the EA is now requiring that any proposed AD facilities have an approved odour management plan before being granted a licence to operate. This will further help the industry to raise its standards and prove that, as a green solution for society, AD is here to stay and will only improve.
The UK generates 14.8 million tonnes of food waste each year, yet many AD facilities are struggling to access this feedstock. Without more Government support for food waste collections, we run the risk of plants failing, financially and operationally. So Biffa is working hard to convince the Government that separate food waste collections from homes and businesses is the right way to go. We would encourage operators to review their odour management systems and procedures, and to learn from what has been, at times, a challenging process. Despite separate food waste collections being unsupported by the main political parties, the Green Investment Bank’s recent report Smarter, Greener Cities:
Ten Ways to Modernise and Improve UK Urban Infrastructure highlights AD as ready to be “rolled-out immediately and at scale across the country”. Tackling the technology weak spots will pay dividends, particularly issues of odour release in urban settings. The EA is right to insist that odour management plans are approved as a prerequisite to new AD developments. If AD is to fulfil its potential as the poster child for low-carbon Britain, we all need to play our part in protecting its reputation and delivering excellence.
Dr John Casey is Energy Division managing director at Biffa Economies of scale made it possible Compared with most AD facilities in Europe, Poplars is a giant. It treats 120,000 tonnes of food waste each year and generates 6.5MW of renewable energy, enough to power 15,000 homes.
The scale of Poplars has made Biffa’s investments possible, and it is important that the company helps the industry to follow in its footsteps.
Controlling sources of odour In order of priority:
1 Eliminating or reducing the source of the odour
2 Disrupting the transmission pathway to site boundary 3 Actively capturing and treating the odour, or increasing dilution and dispersion.
This project brought the plant under the national spotlight and cemented its status as one of the UK’s most influential green ventures. When the company took over the facility from its building and commissioning contractors, it was falling well short of its contractual requirements for odour control. The biofilters designed and built to treat odorous air from the plant were not fit for purpose, and created a focal point of dissension from residents and the regional Environment Agency (EA) team. As any operator of a waste facility will know, protecting neighbours from unwanted environmental effects is a crucial part of fostering acceptance and responsible long-term engagement with local residents and businesses. In the Poplars case, residents – some of whom lived just 200m from the plant – were disappointed about the level and frequency of odour escaping from the plant. Biffa was thereby obligated to develop a robust and bespoke solution for long-term community harmony. With board-level commitment from Biffa to invest in an exemplar facility, we had the in-house skills to make it happen.
The EA had no template or predefined standards for an odour management plan for AD, so it took the company’s in-house engineering team to come up with the solution. Poplar AD 1 They researched across other industries to establish best practice in technologies and management procedures, gradually drafting the odour management plan step-by-step. Sampling and testing each possible source of odour, and then benchmarking against best available technologies, the team finally engineered a robust odour management system for the Poplars site. Biffa invested in a novel vortex scrubber system which uses a combination of speed, turbulence and moisture to separate volatile organics (odorous compounds) from the air stream.
The removal rate of the vortex scrubber is far superior to that of a conventional scrubber: its installation made a significant and lasting improvement. Pre-treated air from the vortex scrubber was then passed to the main odour control treatment plant, providing a double barrier to odour escape. While this provides an effective abatement solution, further works were needed to ensure robust 24/7 operations.
Once the new scrubber was installed, addressing any remaining odour followed the law of diminishing returns. The team introduced systems, procedures and equipment to tackle the challenge. There was no single cure, so the final plan included aspects of training, housekeeping, instrumentation, controls, maintenance and system management. Despite the years of challenging problems,
Biffa has addressed the issues head on, investing a further £4m in process improvements at Poplars. This demonstrates the value that the company places on this flagship facility. The conditions and checks set out in the detailed odour management plan ensure that the plant operates to the highest possible standards and achieves mini-mal impact on the local environment. The Poplars team is now proud to have received zero compliance assessment reports from the EA in the past 12 months, as well as a dramatic fall in odour complaints.
Poplar AD 2 Taking three years and 15 drafts, the odour management plan was finally approved by the EA in March 2015. The improvement has elevated Poplars AD to a ‘best in class’ status with the EA. It is a UK first for such a facility and sets an example for others in the industry to follow. Lisa Pinney, EA area manager for West Midlands, said: “Biffa has made significant investment at the Poplars site. Through 2014, the AD plant has operated not only in line with its permit but also best practice for the industry, which shows what can be achieved when we work together well.” The Poplars management plan is now being used as a template for Biffa’s mechanical biological treatment facility in West Sussex, and is publicly available on the EA website for other AD developers and operators to learn from. Following this experience, the EA is now requiring that any proposed AD facilities have an approved odour management plan before being granted a licence to operate. This will further help the industry to raise its standards and prove that, as a green solution for society, AD is here to stay and will only improve.
The UK generates 14.8 million tonnes of food waste each year, yet many AD facilities are struggling to access this feedstock. Without more Government support for food waste collections, we run the risk of plants failing, financially and operationally. So Biffa is working hard to convince the Government that separate food waste collections from homes and businesses is the right way to go. We would encourage operators to review their odour management systems and procedures, and to learn from what has been, at times, a challenging process. Despite separate food waste collections being unsupported by the main political parties, the Green Investment Bank’s recent report Smarter, Greener Cities:
Ten Ways to Modernise and Improve UK Urban Infrastructure highlights AD as ready to be “rolled-out immediately and at scale across the country”. Tackling the technology weak spots will pay dividends, particularly issues of odour release in urban settings. The EA is right to insist that odour management plans are approved as a prerequisite to new AD developments. If AD is to fulfil its potential as the poster child for low-carbon Britain, we all need to play our part in protecting its reputation and delivering excellence.
Dr John Casey is Energy Division managing director at Biffa Economies of scale made it possible Compared with most AD facilities in Europe, Poplars is a giant. It treats 120,000 tonnes of food waste each year and generates 6.5MW of renewable energy, enough to power 15,000 homes.
The scale of Poplars has made Biffa’s investments possible, and it is important that the company helps the industry to follow in its footsteps.
Controlling sources of odour In order of priority:
1 Eliminating or reducing the source of the odour
2 Disrupting the transmission pathway to site boundary 3 Actively capturing and treating the odour, or increasing dilution and dispersion.
Tuesday, April 14, 2015
: Environment Protection Authority orders New abattoir near Darwin on the nose to fix odour problem
The Northern Territory's Environment Protection Authority (EPA) has ordered Australia's biggest beef producer to take "immediate action" to solve odour problems emanating from its new abattoir near Darwin.
Residents living near the Australian Agricultural Company's (AACo) meatworks at Livingstone, have been complaining about bad smells for months.
Speaking to ABC News last month, resident Glenn Spears described the smell from the abattoir site as "rank".
"We've been experiencing some pretty terrible smells coming from that direction," he said.
"Even when it's a really still morning, the smell... it's just a rank smell that's hanging in the air.
"This morning it was almost sickening to smell, it was that bad."
The odour is being caused by the poor quality of wastewater being used, and perhaps over-used, by AACo for irrigation.
The EPA said it had comprehensively discussed AACo's proposed plan for improving the quality of wastewater used for irrigation and after "lengthy consideration and discussion", had issued a direction to AACo under the Waste Management and Pollution Control Act, directing the company to "immediately take measures to prevent offensive odours."
EPA chairman Bill Freeland, said the authority had given AACo permission to start processing cattle late last year knowing the smell could become an issue.
"We in good faith discussed it with them and they said they needed to start slaughtering cattle so they could test and fine-tune their system," Dr Freeland said.
"We actually didn't believe they had a system that could be fine-tuned sufficiently, but over six months we felt they could make some great progress.
"Unfortunately that progress really didn't eventuate.
"But now, AACo has bitten the bullet and is launching into a big program to fix it all up.
"The other thing that's very important, is that there'll be no further increase in the number of head that can be slaughtered per day, they (AACo) volunteered that, and we'll have to keep them to that.
"The cap is 250 head [a day], maximum."
In a statement, AACo said it had met with the NT Environment Protection Authority a number of times and has presented a plan to mitigate odours and ensure sustainable compliance with the EPL for the Livingstone Beef processing facility south of Darwin.
"AACo is complying with the direction from the NTEPA and keeping them informed of progress," it said.
Last month, the company's managing director, Jason Strong, told ABC Rural the odour problem would be fixed.
"It's something we're very conscience of and working on and its' something that we'll be fixed, there's no question about that, it's going to be fixed," he said.
"This is a multi-decade investment for us and we want to be a good part of the community for a long time.
"This is not a good experience for the locals, but we will fix it and make sure that we don't have a negative impact on the local environment."
Steps To Address Odor Issues @ La Jolla
It's an issue that lingers in La Jolla like a bad odor.
The unpleasant smell left by sea lions and birds at La Jolla Cove is again in the news with a judge having decided the city of San Diego is not responsible for solving the problem.
The La Jolla Town Council will hold a hearing Thursday on the next steps in the ongoing battle against the smell left by accumulated animal droppings.
Steve Haskins, La Jolla Town Council president, said the smell hurts the nearby businesses.
“It (the smell) has a lot to do with the direction the wind is going,” Haskins told KPBS Midday Edition on Wednesday. “Unfortunately, it goes up to Prospect Street where the businesses are located. They say it’s a huge problem for them to keep customers, especially in the outdoor restaurants.”
Last month, a Superior Court judge ruled against a group of La Jolla business owners, saying the city doesn't have a duty to control any nuisance caused by wild animals and isn't the cause of the odor.
Citizens for Odor Nuisance Abatement, the group that filed the lawsuit, said it plans to appeal.
But Norm Blumenthal, an attorney who represents the group, said the damage has already been done.
“It’s adversely impacting their businesses,” Blumenthal said. “We’re noted as the most beautiful city in America that stinks. That’s not a very good reputation. This is an issue of health and safety.”
City spokesman Bill Harris said the city has recently contracted with marine mammal expert Doyle and Associates to "explore what conditions exist within this colony of sea lions that may provide alternatives for changing behaviors or otherwise reducing the colony’s impact on the bluffs."
Doyle and Associates is expected to deliver a preliminary report in a few months.
The city also plans to continue the application of a microbial spray until a more permanent solution is found, Harris said.
The hearing is open to the public and will take place at 5 p.m. Thursday at the La Jolla Recreation Center at 615 Prospect St.
Please stay on topic and be as concise as possible. Leaving a comment means you agree to our Community Discussion Rules. We like civilized discourse. We don't like spam, lying, profanity, harassment or personal attacks.
East Bay residents report mysterious gas odor
Pacific Gas & Electric Co. is looking into a mysterious gas odor that prompted numerous calls from concerned residents in Contra Costa County on Monday morning.
Starting around 9 a.m., the utility began fielding calls from the public reporting the smell of natural gas along the Highway 24 and Interstate 680 corridors, said Tamar Sarkissian, a PG&E spokeswoman.
Crews were dispatched to each caller’s locations with testing equipment, but found no evidence of natural gas, Sarkissian said. The calls tapered off, she said, with the last reports coming in around 10:30 a.m.
Investigators were looking into what could have caused the odor, but it did not appear that a gas leak was the culprit, she said.
Thursday, March 12, 2015
Subscribe to:
Posts (Atom)